Multipurpose Segmented Sacrificial Anodes
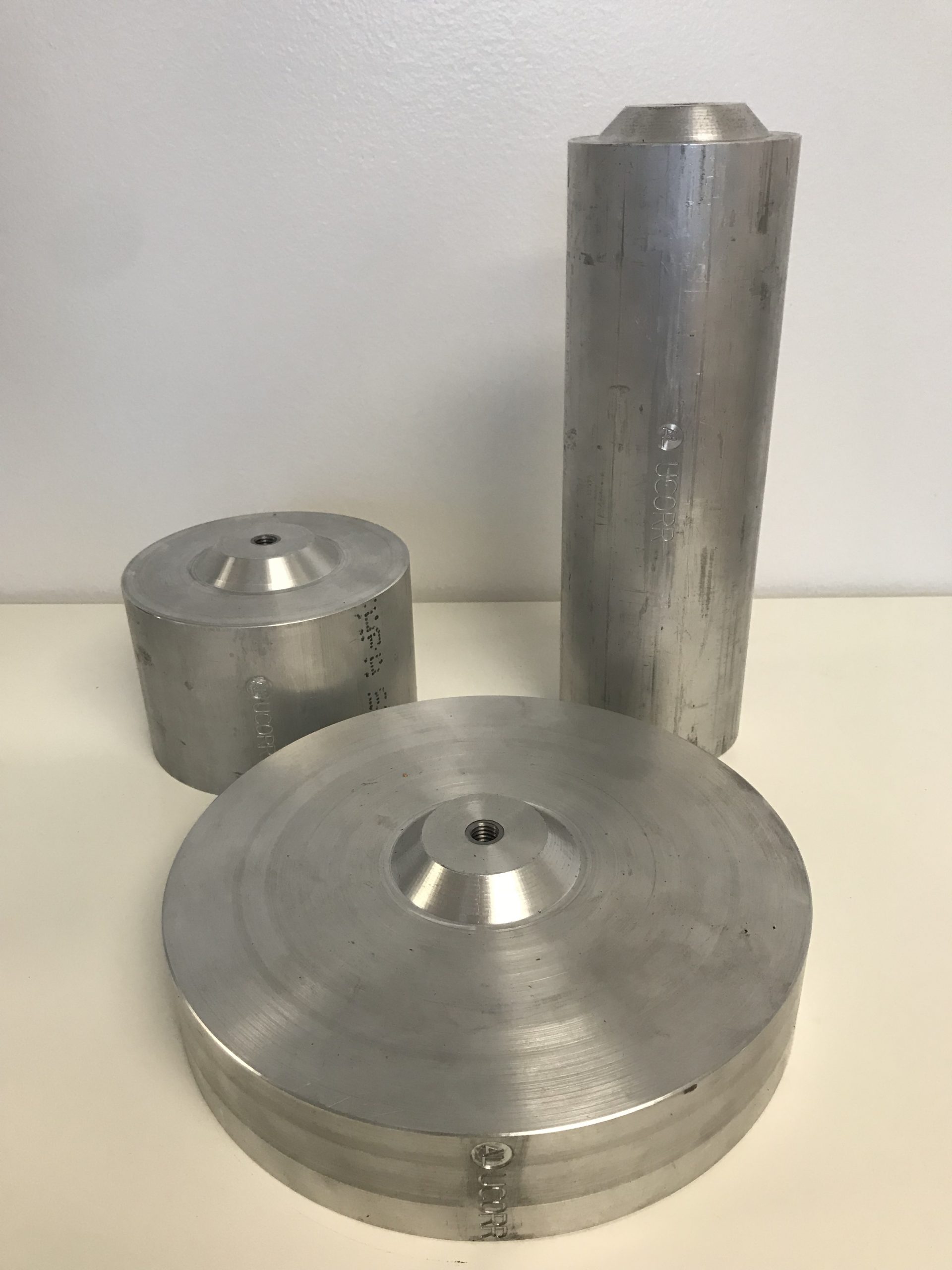

There are a wide variety of sacrificial anodes, depending on the application, in terms of weight and shape. The large variety of anode types creates complications in selecting the most suitable shape and weight for the intended application. Sacrificial anodes available in the market have fixed shapes and weights, depending the application. These factors are utilized to calculate the life and resistance of the anode(s).
Depending on the location of the protected structure (soil or liquid applications), the type of protective coating, and the corrosiveness of the environment, designers face difficulties with design calculations, alloy selection, shape selection, and installation procedures. Sacrificial anodes utilized in marine environments (usually aluminum and zinc alloys) are attached to structures utilizing various welding procedures. Marine anodes are typically large and heavy due to high current requirements associated with seawater. Installation and maintenance costs are considerable as installation often requires cranes, divers, underwater welders, etc.
The innovative Multipurpose Segmented Sacrificial (MSS) Anodes were designed with three simple shapes/weights, which are manufactured utilizing standard sacrificial anode alloys that can be customized for use in all environments. Designers can customize the weight and surface area of sacrificial anode systems by simply stacking them together, as necessary. The surface area factor determines the electrical resistance of the system and consequently the current output capacity of the system and the weight factor determines the life of the system. The MSS anodes are designed to achieve complete customization to fulfill the design requirements in any scenario.
Due to its special design, all MSS Anode segments can be connected and tightened together utilizing applicable couplings and fittings installed at either end segment to achieve the desired surface area and weight. CP system design current output and weight can be easily achieved by customizing the quantity/arrangement of segments utilized. The convex/concave ends of each anode segment are designed to create a seal/lock when stacked upon each other and act as an integrated, single anode.
The most common active metal alloys utilized for MSS anodes are :
Depending on the location of the protected structure (soil or liquid applications), the type of protective coating, and the corrosiveness of the environment, designers face difficulties with design calculations, alloy selection, shape selection, and installation procedures. Sacrificial anodes utilized in marine environments (usually aluminum and zinc alloys) are attached to structures utilizing various welding procedures. Marine anodes are typically large and heavy due to high current requirements associated with seawater. Installation and maintenance costs are considerable as installation often requires cranes, divers, underwater welders, etc.
The innovative Multipurpose Segmented Sacrificial (MSS) Anodes were designed with three simple shapes/weights, which are manufactured utilizing standard sacrificial anode alloys that can be customized for use in all environments. Designers can customize the weight and surface area of sacrificial anode systems by simply stacking them together, as necessary. The surface area factor determines the electrical resistance of the system and consequently the current output capacity of the system and the weight factor determines the life of the system. The MSS anodes are designed to achieve complete customization to fulfill the design requirements in any scenario.
Due to its special design, all MSS Anode segments can be connected and tightened together utilizing applicable couplings and fittings installed at either end segment to achieve the desired surface area and weight. CP system design current output and weight can be easily achieved by customizing the quantity/arrangement of segments utilized. The convex/concave ends of each anode segment are designed to create a seal/lock when stacked upon each other and act as an integrated, single anode.
The most common active metal alloys utilized for MSS anodes are :
- Magnesium Alloys
- Pure magnesium alloys: 1.75 V driving voltage.
- Standard magnesium alloys: 1.55 V driving voltage.
- Zinc Alloys
- Mil Spec A-18001K
- ASTM B-418 Type2
- Aluminum Alloy III
Soil Application:
Marine Application:
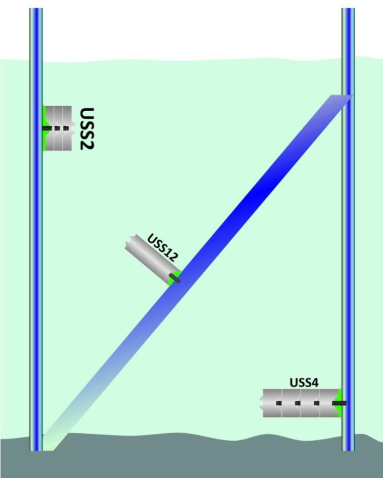
Reservoir Application:
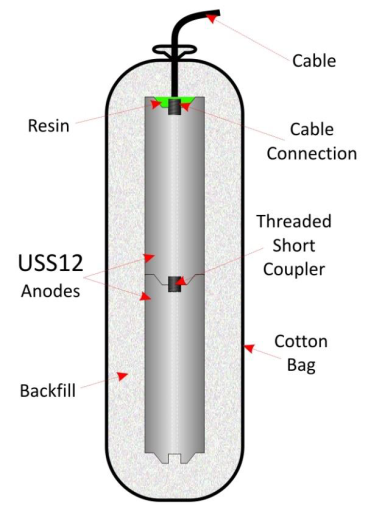
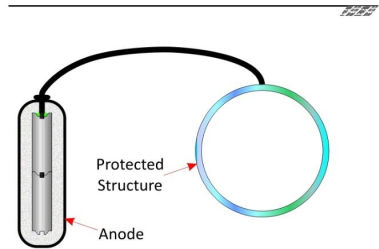
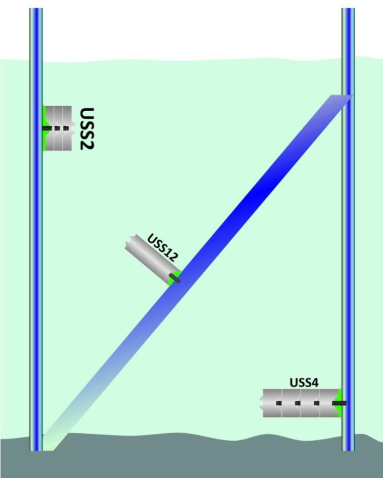
Reservoir Application:
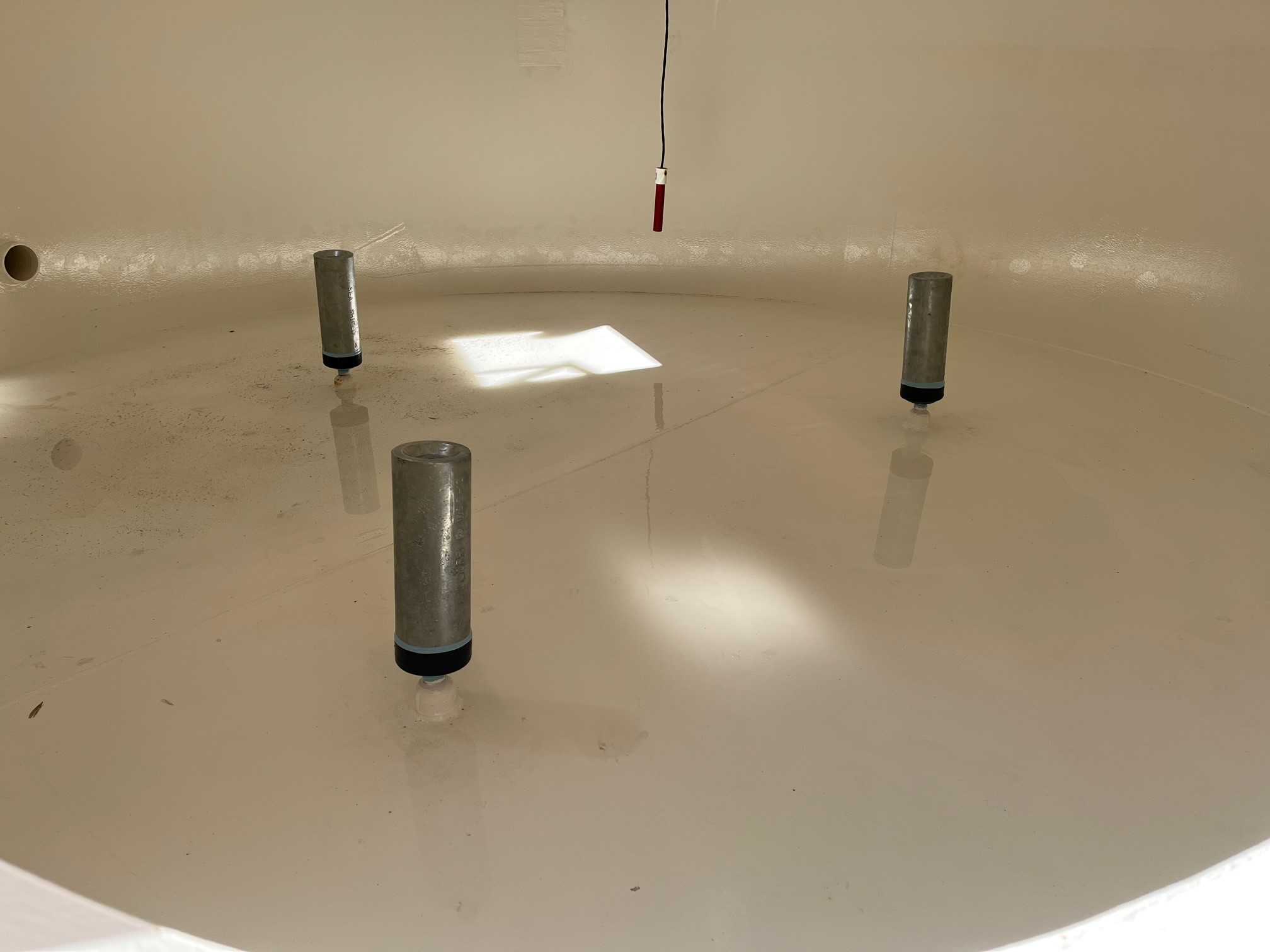
The advantages of utilizing Ucorr® MSS Anodes with respect to conventional anodes are prioritized as follows:
- The current output and resistance of each MSS Anode type can easily be adjusted based on design requirements. In other words, the design engineer can easily customize integrated MSS Anodes as desired.
- Significant cost reductions associated with installation, maintenance, and replacement, especially replacement of anodes in liquid applications.
- Reduces cost of supplying anodes up to 30%.
- Minimizes damage to protective coatings and structures due to minimal welding requirements for liquid applications.
- Increases strength/reliability of electrical/mechanical connections.
- Reduces drilling requirements in soil applications due to capability of adjusting anode surface area/weight, which minimizes required drilling locations and subsequently, land acquisition costs.
- Reduces costs of production, storage, and transportation.
Ucorr’s Recommended Sacrificial Anode Material Selection Protocol:
- Magnesium Alloys
- Electrolyte pH greater than 5.
- Concentration of chloride ions is not considerable.
- Liquid resistivity is greater than 2,000 Ω-cm.
- For resistivity greater than 5,000 Ω-cm, high-potential magnesium alloys should be selected.
- Zinc Alloys
- Concentration of carbonates and bicarbonates is not considerable.
- Temperature is less than 120°F (50°C).
- Aluminum Alloys
- Chlorine ion concentration is greater than 1,800 ppm.
- Temperature is between 120°F & 212°F (50°C & 100°C).